Ever wondered what kind of structures make up the skyline of your city? Commercial buildings, those towering giants and bustling hubs of activity, are constructed using a range of methods. Understanding the various types of commercial construction can be a bit like peering into a detailed manual of modern architecture and engineering.
Most commercial buildings fall into a few common categories based on the construction materials and techniques. Steel frame structures are among the most prevalent, particularly for taller skyscrapers and expansive warehouses. Their strength and flexibility make them a go-to choice for many developers.
Concrete buildings, on the other hand, offer durability and are often used in constructing everything from schools to shopping malls. The versatility of concrete allows for a range of architectural designs while keeping costs manageable.
- Introduction to Commercial Construction
- Steel Frame Structures
- Concrete Buildings
- Pre-fabricated Construction
- Sustainable Building Practices
- Technological Advances in Construction
Introduction to Commercial Construction
When we talk about commercial construction, we’re diving into a vast field that encompasses the creation of spaces dedicated to business purposes. These buildings are designed for a variety of uses, including offices, hospitals, malls, and hotels. Essentially, anything that isn't residential but involves making money can be classified as commercial construction.
Unlike residential construction, where the focus is primarily on creating a cozy home for families, commercial buildings prioritize function and efficiency. They're built to handle large crowds, support heavy equipment, and often need to be easily modified to fit changing business needs. Not to mention, they must adhere strictly to codes and standards to ensure safety and accessibility for everyone.
Types of Commercial Construction Projects
Understanding the scope of work in commercial construction starts with recognizing the different types of projects. These can range from small-scale endeavors, like renovating a corner shop, to massive undertakings, like erecting a new hospital or high-rise office building.
- Small-scale projects: These include renovations, expansions, or repairs on existing structures. While they might be less complex, they often require precise coordination to minimize disruptions to ongoing business operations.
- Medium-scale projects: This might involve constructing new facilities, such as strip malls or small office buildings. These projects often have a clearly defined budget and timeline, requiring methodical planning and execution.
- Large-scale projects: Think of big infrastructure, such as airports, skyscrapers, or extensive commercial complexes. These are the most complex projects in the field, involving multiple stakeholders, significant budgets, and extended timelines.
Let's take a look at a snapshot of how construction spending is distributed across different sectors:
Sector | Spending in Billions |
---|---|
Healthcare | 45 |
Retail | 60 |
Education | 25 |
Working in this domain requires understanding how these factors play into the planning and construction process. It's not just about building a structure; it's about crafting a space that meets specific commercial needs efficiently and effectively.
Steel Frame Structures
When it comes to commercial construction, steel frame structures are like the unsung heroes of the modern cityscape. They've got this incredible ability to withstand heavy loads, making them perfect for high-rise buildings and expansive commercial spaces like shopping centers and warehouses.
The secret sauce of steel? It's all about its strength-to-weight ratio. Steel frames can handle enormous weights without being heavy themselves, which makes them super reliable and economical for creating large open spaces. Ever notice those modern office buildings with wide windows and minimal columns? Thank the steel frames behind the scenes.
Why Choose Steel?
Developers often opt for steel because of its durability and flexibility. In areas prone to earthquakes, steel’s flexibility helps buildings sway rather than crack under stress. It's why California, with its seismic activity, often uses steel in its construction.
And let's not forget about the speed. Pre-fabricated steel sections can be quickly assembled on-site, significantly cutting down construction times. It's like giant puzzle pieces coming together to create a sturdy, impressive structure.
Environmental Impact
With the focus on sustainability these days, steel also scores brownie points for being recyclable. Up to 90% of structural steel is made from recycled material. Plus, its longevity reduces the need for frequent rebuilds, saving resources in the long haul.
Quick Facts
- Versatility: Can be molded into any shape for innovative design.
- Construction Speed: Prefabricated segments make the building process faster.
- Recyclability: A super green choice, as steel is highly recyclable.
Overall, steel frame structures are foundational in modern construction, offering a balance of strength, flexibility, and sustainability essential for any commercial construction project.
Concrete Buildings
When it comes to commercial construction, concrete buildings have a reputation for durability and strength. You see them everywhere—from those sturdy retail centers to big city schools. What makes concrete such a popular choice? Let's dig into the details.
Why Choose Concrete?
Concrete is incredibly versatile. It can be molded into a variety of shapes and sizes, which allows architects to get creative. Apart from design flexibility, it’s strong enough to withstand natural disasters like earthquakes and hurricanes, a crucial feature for many commercial buildings.
- Durability: Concrete structures are built to last. They can endure tough weather and even fires, making them a safe bet for long-term investments.
- Cost-effective: While the initial cost can be high, the long lifespan and low maintenance needs often make up for it. Over time, concrete buildings can turn out to be budget-friendly.
- Energy Efficiency: Concrete's thermal mass helps regulate indoor temperatures, leading to lower energy bills.
Common Types of Concrete Constructions
Commercial buildings make use of several concrete construction techniques. You might spot some difference in method depending on the size and purpose of the building.
- Precast Concrete: Made in a factory and transported to the site, ensuring a consistent quality. It's often used in constructing parking garages and stadiums.
- Cast-in-Place Concrete: Poured directly on-site, it offers a seamless build, making it ideal for projects like bridges or highways that need non-stop support.
- Pre-stressed Concrete: Reinforced with tensioned steel cables, it’s primarily used in large-span structures like bridges or aircraft hangars.
According to a 2023 industry report, nearly 60% of new commercial buildings in urban areas are opting for concrete due to its flexibility and resilience. With a big emphasis on sustainability, construction methods continue to evolve, introducing more eco-friendly techniques into the mix.
Challenges with Concrete
Of course, it’s not just sunshine and rainbows. Some drawbacks come with concrete usage.
- Weight: Concrete is heavy, potentially adding challenges during transportation and construction.
- Environmental Impact: Producing concrete releases a significant amount of CO2. Industries are working on 'green concrete' to address this.
Overall, concrete remains a heavyweight contender in the field of commercial buildings, balancing benefits and challenges with innovation and practicality.
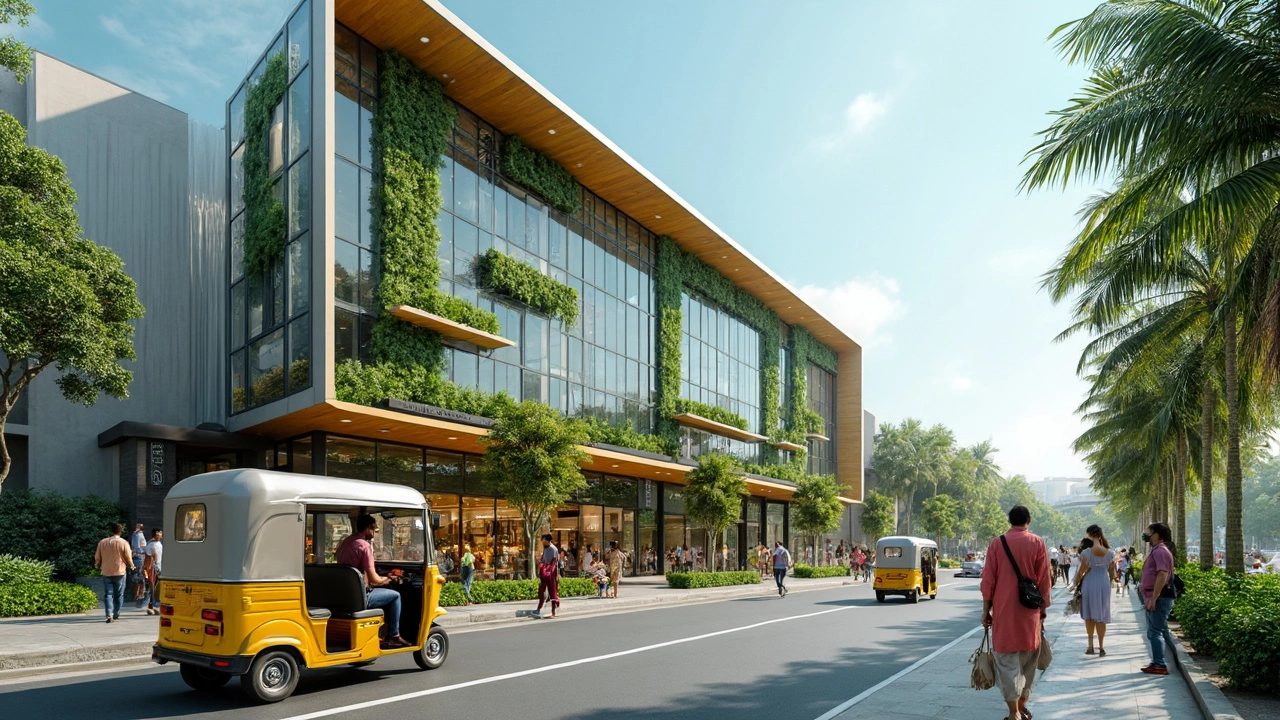
Pre-fabricated Construction
Pre-fabricated construction, often just called prefab, is essentially building off-site. Imagine assembling giant LEGO pieces but on a construction scale. In the world of commercial construction, this method is gaining traction because of its speed and efficiency.
So how does it work? Large sections of a building, like walls or even entire rooms, are manufactured in a factory. They’re then transported to the construction site where they’re swiftly assembled. This approach reduces on-site labor and typically results in less waste, which is a win for contractors looking to save on costs.
A huge plus for prefab is its potential to be more eco-friendly than traditional construction. Factories can better control conditions, leading to a more efficient use of materials. Plus, any leftover materials from one project can be recycled into the next batch, cutting down overall waste.
The Rise of Pre-fab in Commercial Spaces
Looking at some numbers, the prefab construction industry is expected to boom in the next few years. A report by Market Research Future predicts the market will reach $135 billion by 2026. This growth is largely driven by demand for construction that is not just faster but also more sustainable.
Prefab is not just for single-story buildings or sheds; many modern high-rises incorporate pre-fabricated elements. An interesting example is the Marriott hotel in New York, which was built using a significant amount of prefab components, cutting construction time in half.
Given the benefits, it's no wonder commercial developers are turning to pre-fab methods more often. They get buildings up quicker, often with less hassle, and sometimes at a lower cost. As we look to the future, it’s pretty likely that pre-fab will play an even bigger role in shaping our cityscapes.
Sustainable Building Practices
Sustainability in commercial construction isn't just a buzzword—it's rapidly reshaping how we think about building design and execution. The need for environmentally friendly and energy-efficient commercial buildings has grown immensely over the past few years as businesses become more aware of their ecological footprint.
Eco-Friendly Materials
One way to achieve sustainability is by using eco-friendly materials. Bamboo, reclaimed wood, and recycled steel are popular choices that not only reduce waste but also provide durability. These materials are often used in interiors to add warmth and character without compromising on environmental goals.
Energy Efficiency
Energy efficiency is another pillar of sustainable construction. Many commercial buildings now employ smart systems that gauge energy use and automatically adjust to save power. LED lighting and solar panels have become the norm for reducing electricity bills and lessening environmental impact.
Water Conservation
More projects are integrating water efficiency into their design. Low-flow fixtures, rainwater harvesting systems, and greywater recycling reduce water consumption significantly. Some innovative designs even collect rainwater for landscape irrigation, making the building more self-sufficient.
LEED Certification
LEED (Leadership in Energy and Environmental Design) certification has become a benchmark for sustainable buildings. It provides a framework that project teams can follow, assessing the sustainability of a project from start to finish.
With incentives such as tax breaks and energy savings, adopting sustainable practices in commercial construction isn't just good for the planet—it's financially savvy too.
Impact on Property Value
Build it green, and they'll come—or so the saying goes. Sustainable commercial buildings are more attractive to tenants and buyers, often leading to higher property values. Plus, these buildings typically enjoy lower operating costs in the long term.
Whether you're a developer or someone interested in construction trends, understanding sustainable practices is crucial. The more we embrace them, the better our built environments will be for the planet and future generations.
Technological Advances in Construction
Technology is shaking up the commercial construction world in ways you might not even realize. If you've ever walked by a construction site and noticed all sorts of high-tech gadgets and gizmos, you're not alone. There's a lot more than just hammer and nails going on.
Building Information Modeling (BIM)
BIM is like having a virtual blueprint of a building. It’s become vital in construction methods, offering a 3D model that encompasses every aspect, from structural elements to electrical systems. Basically, it helps everyone involved to get a crystal-clear view of what’s going on, cutting down on miscommunication and cost overruns.
3D Printing
3D printing isn't just for small-scale prototypes anymore. In the realm of commercial buildings, it's revolutionizing how parts and components are manufactured. Imagine being able to 'print' a building component right on site. This tech speeds up construction and slashes waste.
Wearable Tech and Drones
Advances in wearable technology mean workers are safer and more efficient than ever. From smart helmets to location trackers, these gadgets add a layer of safety on the site. Drones, on the other hand, are turning into the ultimate inspectors, offering aerial views that help in planning and monitoring construction work.
Green Building Technologies
The push for sustainable construction is real, and technology is leading the charge. Smart energy systems, water-efficient plumbing, and eco-friendly materials are now common. These innovations not only reduce environmental impact but also cut costs in the long run.
Technology | Benefit |
---|---|
BIM | Improved design accuracy |
3D Printing | Reduced waste and time |
Drones | Enhanced site surveys |
Wearables | Increased worker safety |
In short, these tech trends are not just making construction faster and cheaper; they're transforming the entire landscape. So next time you glance at a glitzy mall or towering office block, you’ll know there’s some serious tech wizardry behind those walls.
Written by Fletcher Abernathy
View all posts by: Fletcher Abernathy