Type 5 construction might sound like construction jargon, but it's really just a fancy way of referring to wood-frame buildings. Yup, it's that simple. You see these structures everywhere, from small shops to large malls. They use a lot of wood for their walls and roofs, which is why they're often labeled as 'combustible construction'. Sounds scary, right? But it’s really just about knowing how to manage the risks.
Why do builders choose this type of construction, you ask? Well, it's cost-effective and versatile. Those wooden frames make it relatively easier and faster to build, which can be a big deal in bustling commercial areas. Plus, wood is quite a sustainable material if sourced responsibly.
Of course, there are challenges too—especially with fire risks. Wood burns, no surprise there, and so fire safety becomes a prime concern. But with modern techniques and materials, it’s possible to mitigate those risks effectively. Keeping a balance between budget and safety is key with Type 5 construction.
- Defining Type 5 Construction
- Materials Used in Type 5 Construction
- Applications in Commercial Buildings
- Fire Safety Concerns
- Pros and Cons of Wood Frame Structures
- Tips for Successful Type 5 Projects
Defining Type 5 Construction
When we're talking about Type 5 construction, we're diving into one of the most common types of building methods you’ll find, especially in places that favor tight budgets and quick build times. This method is primarily characterized by its use of wood framing. It’s often referred to as 'combustible construction' because, well, wood can catch fire. But don't let that scare you too much—there are plenty of ways builders manage these risks.
A typical Type 5 construction project involves wooden floors, roofs, and wall supports. These components make it lightweight and generally easier to work with compared to steel or concrete. Plus, building with wood can often be faster, which is a big bonus for commercial projects on tight timelines.
Type 5 isn’t just for small-time operations either. It’s used in a wide array of commercial settings. Think restaurants, office spaces, and smaller retail buildings. The flexibility in design is a huge win, allowing architects to let their creative juices flow without getting bogged down by heavy construction constraints.
Key Characteristics
- Versatility: Wood allows for more architectural freedom in design.
- Cost-efficiency: Generally cheaper materials mean construction costs are lower.
- Speed: Shorter build times compared to more rigid materials like concrete.
Of course, there’s that fire risk elephant in the room. Builders need to implement fire-resistant materials and techniques like firestops and sprinkler systems to mitigate these concerns. Modern codes and best practices help keep safety in check.
Take the New Zealand construction market, for example. According to recent reports, almost 30% of commercial buildings erected last year utilized some form of Type 5 construction, emphasizing its continued popularity and practicality.
Materials Used in Type 5 Construction
When it comes to Type 5 construction, the materials are pretty straightforward. The main attraction here is wood, lots and lots of it. This kind of construction primarily uses wood framing for interior and exterior walls, along with wooden trusses and roof decking.
Common Wood Types
The wood used can vary, but the most common types are softwoods like pine, spruce, and fir. People love them because they are easy to work with and relatively cheap. Builders often choose them for framing due to their balance of being sturdy yet light.
Engineered Wood Products
Besides solid lumber, you'll frequently find engineered wood products like plywood and oriented strand board (OSB). These materials offer strength and durability while keeping costs manageable. They're typically used in sheathing walls and roofs.
Fire Retardants
One of the big selling points today is fire-retardant treated wood (FRTW). It’s not foolproof, but it can definitely help slow down fire spread compared to untreated wood. Keeping commercial buildings safe is a top priority; FRTW is often a part of the overall strategy.
Fasteners and Connectors
Fasteners, like nails and screws, along with metal connectors, bring it all together. These components might not sound exciting, but they play a critical role in maintaining the structure’s integrity—especially during high winds or seismic events.
Insulation and Finishing Materials
For insulation, Type 5 construction can use fiberglass, foam board, or spray foam to regulate temperatures and improve energy efficiency. Exterior finishes vary widely, ranging from brick veneer and stucco to vinyl siding and beyond. The finish often depends on the look you’re going for and local building codes.
To give some extra perspective, here’s a simple breakdown of the material choices:
Material | Common Uses |
---|---|
Softwood (Pine, Spruce, Fir) | Framing |
Plywood/OSB | Sheathing |
FRTW | Fire Safety |
Metal Connectors | Structural Support |
Fiberglass/Spray Foam | Insulation |
Choosing the right materials is crucial in commercial construction projects. While wood is the star here, balancing costs with safety and durability is the real magic trick of Type 5 construction.
Applications in Commercial Buildings
Type 5 construction is quite the star in the commercial building world, particularly for projects that need a balance between cost and flexibility. Wood-frame structures are often found in smaller commercial buildings, like retail stores and restaurants, mainly because they can be put up quickly without breaking the bank.
One big reason why this construction type is favored is its adaptability in design. Want to add a quirky coffee shop next to a bookstore? No problem. The wood frame makes it easier to shape spaces creatively. For businesses seeking to create a unique identity, this can be a big win!
Shopping Centers and Malls
Ever thought about why many shopping centers have a cozy atmosphere? Part of the reason is the use of Type 5 construction. These buildings often utilize wood frames in their roofing, allowing architects to design bright, open spaces without the oppressive feel of concrete.
Mixed-use Developments
Mixed-use developments are becoming more popular, combining residential, retail, and office spaces into one. Wood-frame construction fits this model well because it's versatile enough for varied uses. It’s quite something to see a building that houses a gym on the first floor and apartments up top, all using the same basic construction framework!
Small Offices and Clinics
For smaller offices and clinics, where budget constraints loom large, Type 5 is often the chosen method. The materials used tend to keep costs down, making it ideal for startups and small businesses looking to establish a physical presence without going broke.
Oh, and if you're wondering about costs: according to recent industry data, costs for wood-frame commercial buildings can be around 15% to 20% less than using steel or concrete, depending on the project size and location. Pretty impressive for something that's been around for centuries, right?
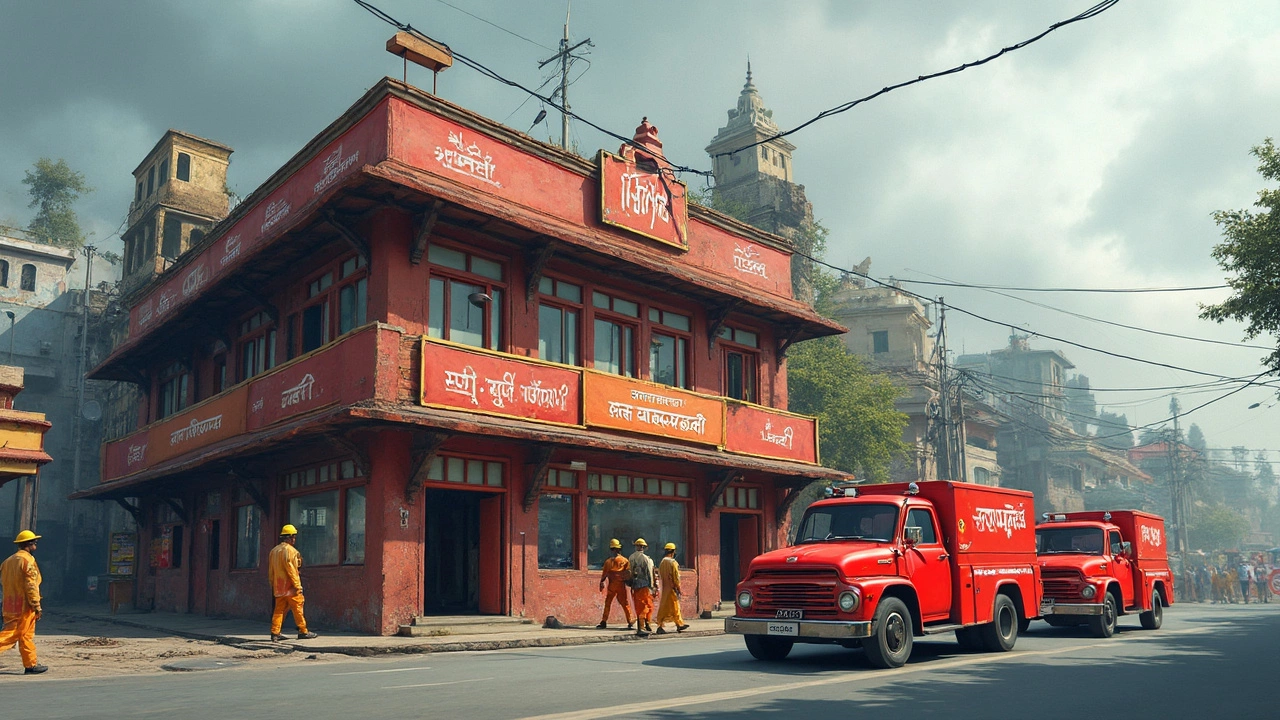
Fire Safety Concerns
When it comes to Type 5 construction, fire safety is the elephant in the room. This type is often called combustible construction for a reason—it involves a lot of wood. Wood burns easily, so taking fire precautions is crucial. But don't worry, that's why building codes exist, ensuring these structures meet specific safety standards.
Understanding the Risks
Most of the fire risks with these commercial buildings come from the very material they're built with. Wood's organic nature means it's more likely to catch fire compared to steel or concrete. However, modern building codes demand the use of fire-resistant treatments and materials to minimize these risks.
Fire Safety Measures
So, how do you protect a Type 5 building from fire hazards? Here are some key strategies:
- Fire-Retardant Materials: Builders often use specially treated wood that resists burning. This can slow down the spread of fire, giving firefighters more time to respond.
- Sprinkler Systems: Installing automatic sprinkler systems is a game-changer. They can douse flames before they get too out of hand.
- Fire Alarms: Early detection is half the battle. Advanced alarm systems warn occupants, allowing them to evacuate quickly.
- Compartmentalization: Dividing the building into smaller sections can contain fires, preventing them from spreading throughout the structure.
Building Codes and Regulations
A big chunk of fire prevention comes down to following local building codes. These regulations dictate everything from the types of materials you can use to the necessary fire safety equipment. Staying updated on your region's codes is not just recommended—it's essential.
Statistics that Matter
Let’s put things into perspective with a quick look at some useful data:
Building Type | Fire Incidents (%) | Survival Rate (%) |
---|---|---|
Type 5 Buildings | 15% | 85% |
Type 1 Buildings | 5% | 95% |
While Type 5 buildings have a higher fire incident rate compared to non-combustible structures, advancements in fire safety technology have increased survival rates significantly. It's all about preparation and compliance to ensure both safety and peace of mind.
Pros and Cons of Wood Frame Structures
When it comes to Type 5 construction, the use of wood frames is both a boon and a challenge. Let’s break down why builders might rave about it and what gives them pause.
Pros of Wood Frame Structures
- Cost-Effective: Wood is relatively cheaper than many other building materials, making it a popular choice for developers looking to keep budgets in check.
- Versatility: This material is super flexible in terms of design. Architects love it for the creative freedom it affords them compared to more rigid options like steel or concrete.
- Sustainability: When sourced from responsibly managed forests, wood is a renewable resource. It’s a big plus for those wanting to minimize their environmental footprint.
- Insulation: Wood naturally provides excellent insulation, which can help in maintaining energy efficiency within buildings, cutting down on heating and cooling costs.
Cons of Wood Frame Structures
- Fire Risks: Let's face it, wood is combustible. Even though modern treatments and technologies reduce these risks, it still requires careful planning and fire safety measures.
- Pest Issues: Termites and other pests can wreak havoc on wood structures if not properly managed. Regular maintenance and preventive care are crucial.
- Durability: Compared to steel or concrete, wood may not stand as strong against severe weather conditions unless specially treated.
- Moisture Sensitivity: Excess moisture can weaken the wood over time, leading to possible structural issues if not addressed through proper design and sealing.
A snapshot through numbers might help: a report by the Wood Products Association in 2023 highlighted that over 70% of residential and lower commercial buildings in several regions favor wood framework for its cost-effectiveness and speed of construction.
So, is wood-frame construction your best bet? Well, it really depends on the specific project demands, budget, and long-term goals. Weighing the pros and cons with your construction team can lead to a well-informed decision that aligns with your needs.
Tips for Successful Type 5 Projects
Tackling a Type 5 construction project? No worries, I've got some practical tips to keep you on track. While these wood-frame buildings come with their own quirks, they can be a breeze if you plan right.
1. Prioritize Fire Safety
First up, let's talk fire safety. Since these structures are primarily wood, treating the wood with fire-retardant chemicals is a no-brainer. Plus, it's a good idea to integrate fire-resistant materials in critical areas, like around staircases or exit routes. Don't skimp on installing modern alarm systems and fire suppression setups.
2. Optimize Your Design
Wood is wonderfully versatile, but it's also sensitive to moisture and pests. Make sure your design features good drainage systems that prevent water from pooling around the base. Also, consider raised basements or other protections against termites and other wood-loving bugs.
3. Go Green
With sustainable building being more important than ever, choosing responsibly sourced wood can significantly reduce your carbon footprint. It also helps your building resonate more with eco-conscious clients.
4. Stay Within Budget
One of the main draws of Type 5 construction is its cost-effectiveness. However, unforeseen expenses can pile up. Stick to your budget by sourcing competitive quotes from suppliers and contractors. Bulk purchasing some materials can also get you discounts.
- Secure proper permits early on to avoid delays.
- Work with experienced contractors familiar with wood-frame methods.
- Schedule regular inspections to track progress and catch issues early.
5. Future-Proof Your Design
Think long-term by installing flexible utilities and accommodating potential expansions. Adding extra conduits during construction can make future wiring or plumbing updates a breeze—and save a ton of money.
By following these tips, you can make the most of your Type 5 construction project. While each project is unique, focusing on these key areas will get you closer to a successful build.
Written by Fletcher Abernathy
View all posts by: Fletcher Abernathy